阐述注塑模具加工的维护保养
来源:admin
浏览:次
发布日期:2020-11-25
注塑模具加工的维护:
1.冷却水道的维护
水冷通道的作用是通过水冷,使塑件在型腔内冷却固化,对塑件的成型过程有很大影响。
冷却水道堵塞的危害:
长时间工作时,冷却水道表面容易沉积水垢、污物、锈蚀等,从而减少了冷却水的流通面积,大大减少了模具之间的冷却水热交换,使其冷却效果大大降低,危害极大。
冷却水道堵塞检查:
冷却水管路表面沉积物增多,将导致管路局部堵塞,通过测量冷却水的流速,可以判断冷却水管路内部情况。计量时,可以在模具和冷却水道之间安装压力控制阀,在相同条件下,通过模具的冷却水压力降也可以进行测定。因此可以判断冷却水道是否被堵塞。如果堵塞到一定程度,要及时清理干净。
冷却水道净化
因冷却水道的设计与型腔形状有关,形状迂回曲折,且不方便拆开,故不能机械地进行清理,只能使用清洗剂进行冲洗,在清洗剂的强力冲力下将粘连的污物清除。清洗剂种类繁多,可供选择。
2.注塑模具卸模的保养
注塑模具加工在完成了一定的生产任务之后,需要从注射机上拆下。拆开后,仔细地清除剩余的塑料,根据不同塑料的不同性质,采取不同的清理方法。普通肥皂水可以用来清除模具内残留的塑料和其它沉积物,然后将模具风干。如果型腔表面有锈斑,应清除,抛光,然后涂上润滑剂保护,然后存放于仓库。
注塑模具加工的故障及排除方法:
注塑模具加工在使用过程中,总会出现或多或少的故障,这些故障对产品质量、生产效率、模具等都会产生不利的影响,下文将对这些问题进行阐述。
1.模具变形及其排除
“模具变形”是指模具在工作过程中,由于弹性变形或塑性形变而造成模具不能正常工作或产品质量不合格的现象,其原因和排除方法如下。
不足之处:
注塑模具加工成型时,模具会受到很大的保压压力,这种压力如果使模具发生永久变形,模具就不能使用,但即使在弹性极限内,模具产生的变形也能恢复,而在变形时,固化成型,则会使开模有困难,甚至不能开模。在这样的情况下,从结构上改造模具已经不可能了,但是可以适当降低注塑压力,或从外侧加框套加强刚性,虽然不好看,倒也可以使用。
模具装配错误:
如果模具装配不当,如模具对中不良,合模处和接合处没有正确对中,这样会使熔体充模不平衡,容易造成模具变形或错位。针对这种情况,应该重新装配模具,对于充模不平衡,有时还可以用修正浇口的方法加以纠正。
2.型腔损伤及其排除
注塑模具加工成型过程中,模腔损伤直接影响制品的质量,模腔损伤是指由于注塑模具加工过程中模塑制品内部表面的硬性损伤,导致表面出现划痕、凹坑、裂纹等缺陷,导致损伤的原因和排除方法如下。
1.硬物损伤型腔:
有时候,开模后取塑件比较困难,就用起子等硬工具勉强去取,这样很容易弄伤其型腔。此外,开模后,不慎将扳手、锤子等硬物掉落型腔内造成型腔损伤。
2.不适当的操作:
如果塑件没有取出,尤其是闭模时,固化后的塑件很容易伤及型腔和模具。
3.修复损坏
损伤后不进行修复就很难继续工作,因此对型腔进行修复的方法有以下几种。
焊接。焊缝修补是一种常用的方法,其中最常见的是气焊。使用电焊时,模具因温度过高易产生变形,甚至开裂,应进行电焊修补,对模具进行预热,焊后进行热处理。
嵌件。对面积小、深度大的破损部位,可加嵌件修补,一般先钻孔再钻入嵌件,钻孔时应注意不打穿冷却水道和螺孔。嵌件与型腔应紧密配合,装好后进行修磨和平整处理。
镀金。对深度小于0.5 mm的缺陷,采用电镀修复,可以镀铜、镀铬,效果更好。
打击。对于材质较软的型腔,可以先在破损部位的背面钻一个盲孔,然后敲击盲孔底部,使破损部位产生凸起;或者在3 mm以外的地方敲击使破损部位产生凸起,再将凸起部分打磨、研磨、抛光。
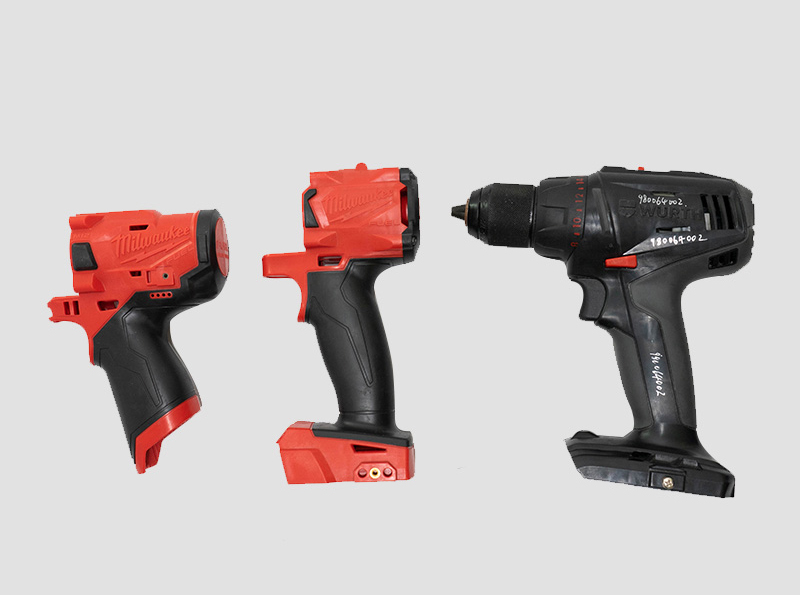
模具锈蚀及其排除
模具多用工具钢制作,在使用时会遇到腐蚀性气体、水等物质引起锈蚀。由锈模制造的塑件会产生质量问题,所以必须排除这些问题。
1.熔融反应产生的气体:
一些原材料加热后会产生挥发性气体,许多原材料在过热时也会产生挥发性气体,这些气体具有多方面的腐蚀性,扩散到机器的周围,当模具失效时,它们就会腐蚀模具。为此,在机器停机时,用软布擦拭模具,并关闭模具,若长时间不用,应在模具腔内喷洒防锈剂,关闭模具时还要涂上黄油,堵住浇口。
2.模具内的冷却水:
模子里多通冷却水来唤醒冷却,所以机器周围有更多的水气。如果把模子冷却到露点,空气中的水分就会在模子的表面结上水珠,如果不及时擦洗就容易生锈。尤其当模具停止工作后,凝结水很快就产生了。所以不要轻易停止成型,即使停止成型,也要关闭冷却水,然后把模具弄干。
3.成型过程中的碳化物:
经过长时间的模具工作后,成型材料析出并分解形成碳化物,经常使模具磨损、腐蚀或生锈。在这样的情况下,如果发现有碳化物产生,应立即用干布擦拭、擦拭。